齿轮减速机振动信号拾取方法的研究
3.1传感器类型的选择
由于齿轮减速机是由齿轮、传动轴和轴承等传动部件及箱体、箱盖等支撑部件红成,传动部件在发生故障时,故障振动频率可覆盖几Hz至数kHz的范围。因此,齿轮减速箱的振动信号不能采用位移和速度传感器来拾取,而只能用加速度传感器来拾取。通常加速度传感器一般采用电荷输出型的压电加速度计,这种加速度计体积小、重量轻、价格便宜。但由于它要和电荷放大器配合使用,因而在传感器与阻抗变换放大器之间就有一段高阻抗信号输送的联接,故降低了系统的低频性能、分辨率、抗干扰能力和稳定性等方面水平。为了改变这种现象,便发展了集成形式的压电传感器-即ICP加速度计,它将阻抗变换放大器封装在传感器的刚性壳体内。
由于齿轮减速机箱体结构的限制,加速度传感器不能安装在箱体的轴承座处,故拾得的振动信号不能很理想反映箱体内的传动元件的振动信号。本章尝试用套在滚动轴承外圈上的套圈应力环来拾取箱体内的传动元件的振动信号。
由于齿轮减速机箱体结构的限制,加速度传感器不能安装在箱体的轴承座处,故拾得的振动信号不能很理想反映箱体内的传动元件的振动信号。本章尝试用套在滚动轴承外圈上的套圈应力环来拾取箱体内的传动元件的振动信号。
3.2 ICP加速度传感器在齿轮减速机振动信号拾取中的应用
典型的集成压电式(ICP)加速度计是在传统的压电加速度计基础上耦合一个以场效应管为核心的内装放大器电路所构成。电路原理如图3-1所示。ICP加速度计除了能带来使用方便操作简化的优越性外,较传统的压电加速度计还具有如下一系列的优点:
1低输出阻抗(《100Ω)。允许使用超长电缆通过恶劣的环境传输信号;
1低输出阻抗(《100Ω)。允许使用超长电缆通过恶劣的环境传输信号;
2固定的电压灵敏度,与电缆的长度和电容量无关;
3作为二线系统,能适应标准的低价格同轴电缆或通用的双导线电缆;
3作为二线系统,能适应标准的低价格同轴电缆或通用的双导线电缆;
4低阻抗的电压输出(±5V),与标准的数据采集系统完全兼容;
5多通道使用时成本更低,只需配置低成本的恒流电压源:
6固有的自测试特点,可通过恒流电压源提供的偏置电压监控传感器的工作正常与否;
6固有的自测试特点,可通过恒流电压源提供的偏置电压监控传感器的工作正常与否;
7大大减少了对测试系统的维护要求。
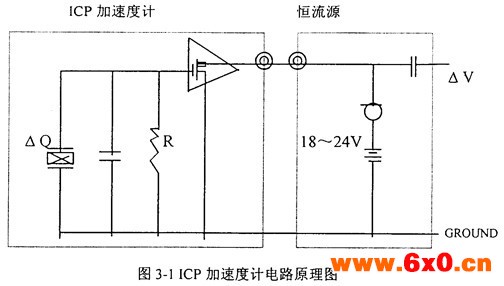
根据上海北智公司推荐,ICP加速度计频响范围的上限频率fmax(Hz)即最高允许频率由以下公式确定:
fmax=(IC-1)×9/2πC×V (3-1)
式中:IC(mA)——恒电流;C(pf)——电缆电容;V(V)——最大信号电压
根据丹麦B&K公司推荐,ICP加速度计与供电电源之间最远导线距离(m):

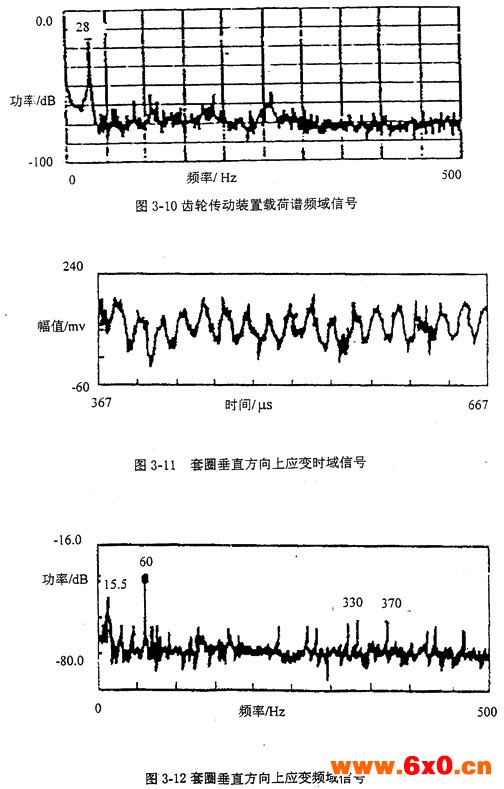
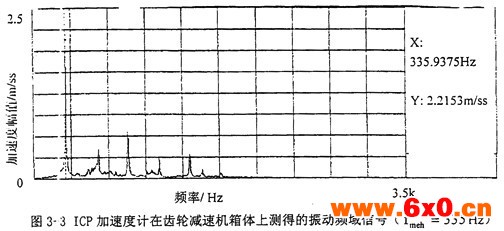
3.3加速度传感器安装位置的确定
为了测得齿轮减速机箱体内传动零部件的故障振动信号,加速度传感器应安装在靠近箱体轴承座处的垂直方向上。但在现场安装加速度传感器往往要受齿轮减速机箱体结构的限制,加速度传感器在箱体的轴承座附近没有合适的位置,有对安装在离轴承座较远处;此外为了节省成本,要求以最少的传感器获得必要沟信息,一台齿轮减速机只能放两到三个传感器。为此可用测试分析仪器通过振动模态等试验对齿轮减速机可能的加速度传感器安装位置进行反复对照比较,既要考虑传感器安装位置能确保齿轮减速机内传动件故障信号的正确处理拾取、振动较强烈,又要考虑该位置刚度相对要大。
采用加速度计监测齿轮减速机这种方法的优点是传感器安装方便,缺点是有时由于箱体结构的限制,传感器不能安装在箱体轴承座附近,且这时候加速度计拾取的振动信号不能全面地反映齿轮传动装置内部轴系部件的损伤情况,另外加速度计的频响范围只能从几Hz至十千Hz,低频响应不是太好,此外,价钱也较贵。
3.4轴承套圈应力环在齿轮减速机振动信号拾取中的应用
为了测得齿轮减速机箱体内传动零部件的故障振动信号,加速度传感器应安装在靠近箱体轴承座处的垂直方向上。但在现场安装加速度传感器往往要受齿轮减速机箱体结构的限制,加速度传感器在箱体的轴承座附近没有合适的位置,有对安装在离轴承座较远处;此外为了节省成本,要求以最少的传感器获得必要沟信息,一台齿轮减速机只能放两到三个传感器。为此可用测试分析仪器通过振动模态等试验对齿轮减速机可能的加速度传感器安装位置进行反复对照比较,既要考虑传感器安装位置能确保齿轮减速机内传动件故障信号的正确处理拾取、振动较强烈,又要考虑该位置刚度相对要大。
采用加速度计监测齿轮减速机这种方法的优点是传感器安装方便,缺点是有时由于箱体结构的限制,传感器不能安装在箱体轴承座附近,且这时候加速度计拾取的振动信号不能全面地反映齿轮传动装置内部轴系部件的损伤情况,另外加速度计的频响范围只能从几Hz至十千Hz,低频响应不是太好,此外,价钱也较贵。
3.4轴承套圈应力环在齿轮减速机振动信号拾取中的应用
本节采用在轴承外圈套圈上拾取应变信号的方法对二级齿轮传动装置箱体所受的动态激励力进行了测试和分析,在此基础上对齿轮传动装置的轴系部件故障进行了诊断。
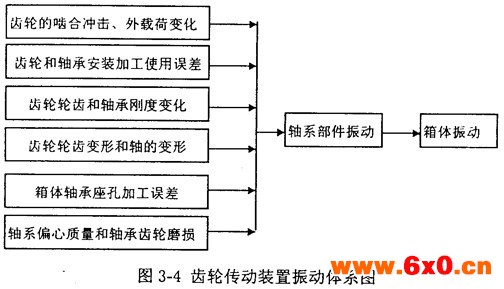
装有齿轮、轴和轴承的轴系是齿轮传动装置的关键部件。在齿轮传动装置的工作过程中,箱体与其内部的轴系部件构成一个振动耦合体系,见图3-4。轴系部件的振动通过轴承激发箱体振动,这样在轴承外圈上安装套圈并粘贴应变片,拾取套圈上的应变信号,也就是对齿轮传动装置箱体所受的动态激励力信号进行测试和分析,就可对齿轮传动装置内的轴系部件进行故障诊断。这种振动测试故障诊断的方法优点是能直接拾取齿轮传动装置内的轴系部件的振动故障信号,频响范围宽,费用低。缺点是需专门制做套圈。
3.4.1测试原理和方法
由齿轮、轴和轴承构成的轴系部件可近似看作是一个线性时变系统,它的振动微分方程组为:

式中:M、C(t)、K(t)分别是轴系部件的质量、阻尼和刚度矩阵,R(t)是外载荷矢量; 、 和q分别是轴系部件有限元集合体的振动广义加速度、速度和位移矢量。
用轴系部件轴的静态变形场模拟轴系部件传动轴弯曲振动振形,可得到轴系部件两端给箱体的动态激励力:
用轴系部件轴的静态变形场模拟轴系部件传动轴弯曲振动振形,可得到轴系部件两端给箱体的动态激励力:
Px=A U, Py=B V (3-4)
式中:Px、Py分别是轴系部件两端给箱体的X方向和Y万向的动态激励力;A、B分别是轴系部件X方向和Y方向的等效刚度矩阵U、V分别是轴系部件上各点的X万向和Y方向的振动位移矢量。从(3-3)、(3-4)式可看出,轴系部件两端给箱体的动态激励力是和轴系部件的质量、阻尼、刚度矩阵以及外载荷矩阵R(t)有关,而外载荷矩阵R(t)是和齿轮的啮合冲击、外载荷变化、齿轮轴承加工误差、齿轮车由承点蚀磨损、齿轮轴承刚度变化等等因素有关。因此在在轴承外圈上安装套圈并粘贴应变片,拾取套圈上的应变信号,也就是直接拾取了齿轮传动装置内的轴系部件的振动故障信号,对该信号进行分析,就可对齿轮传动装置内的轴系部件的故障作出正确的诊断。
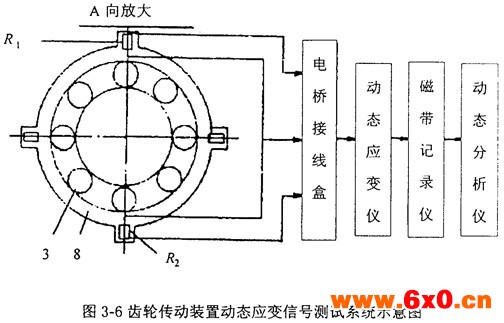
图3-5是被测试的齿轮传动装置传动系统简图,图3-6是测试该齿轮传动装置箱体动态激励力应变信号的系统示意图。零件8为装在轴承外圈上的套圈。套圈把抽系施加给轴承的载荷分成水平方向和垂直方向再传给箱体。如图3-6所示,在套圈的水平和垂直方向分别贴上两片电阻应变片,并分别组成各自的全电桥电路。当轴系产生振动时,轴承对箱体的作用力也随之发生变化,也使贴在套圈上的应变片的电阻值产生变化,而电阻的变化则通过动态电阻应变仪输出电压信号,并经磁带记录仪将此电压信号记录下来。若将所得的信号在动态数字分析仪上进行时域和频域分析,再经过比较,就可对齿轮传动装置内的轴系部件的故障作出较为正确的诊断。
图3-5、3-6中:1-摩擦加载装置;2-412滚动轴承:3-206滚动轴承;4-直流电动机;5-称重传感器:6-406滚动轴承;7-联轴节;8-套圈
3.4.2测试设备和参数
(1)JZQ-250型二级圆柱斜齿轮减速机一台;(2)直流调速电机一台;(3)8通道动态电阻应变仪一台;(4)5OOkg称重传感器一个;(5)TEACMR-30磁带记录仪一台;(6)B&K8200闪光测速仪一台;(7)HP3562动态数字分析仪一台。(8)有偏心质量的弹性联轴节一个。
表1 减速机齿轮几何参数
几何参数
齿轮代号
模数(mm)
齿数
变位系数
齿宽(mm)
螺旋角
精度等级
1
2
Z1=20
0
40
806’34’’
8-8-8
2
2
Z2=79
0
40
806’34’’
8-8-8
3
3
Z3=16
0
60
806’34’’
9-9-9
4
3
Z4=83
0
60
806’34’’
9-9-9
注:电机转速:n=93lrPm;二级圆柱斜齿轮减速机内所有滚动轴承的精度为E级。
3.4.3有关零部件固有频率的计算
预测传动零件及轴承应力套圈固有频率有助于从所测得的动态应变信号中区分出哪些是传动零件的故障频率,哪些是传动零件及轴承应力套圈固有频率,从而可以准确地诊断出那一个传动零件发生了故障。传动零件的有关故障振动频率计算公式见第4章。
(1)仅考虑轮齿的扭转振动齿轮啮合的固有频率
根据ISO圆柱齿轮强度计算标准,轮齿啮合的固有频率计算公式为:

式中:Cr一轮齿的啮合刚度;mred一齿轮副的当量质量。
根据计算,Z1和Z2轮齿啮合的一阶固有振动频率为:fg1=235Hz;Z3和Z4轮齿啮合的一阶固有振动频率为:fg2=272Hz
(2)传动轴(包括齿轮)扭振固有频率
齿轮传动装置中轴系部件传动轴的振动以扭转振动为主,故只计算轴的扭振固有频率。由于信号监测部位在II轴轴承处,故只计算II轴扭振固有频率。
(2)传动轴(包括齿轮)扭振固有频率
齿轮传动装置中轴系部件传动轴的振动以扭转振动为主,故只计算轴的扭振固有频率。由于信号监测部位在II轴轴承处,故只计算II轴扭振固有频率。

上式中:fn1和fn2为II轴一二阶扭振固有频率;Kθ-II轴的扭转刚度;I1、I2-节点两边轴及齿轮的转动惯量。根据计算:fn2=234Hz。
(3)套圈径向振动低阶固有频率计算
由于套圈是直接承受齿轮传动装置箱体动态激励力的零件,且电阻应变片是直接粘贴其上的,因此套圈的共振将直接反映在动态应变信号中。为了准确无误地从动态应变信号中诊断出传动零件的故障信息,必须预测套圈的径向振动固有频率。
套圈是一个不规则的零件,先用有限元按三维八节点实体单元对它进行网格划分,图3-7是有限元网格划分图。边界条件是这样处理的:由于套圈装在减速机箱体孔中时,和孔的配合是过盈配合,且套圈内表面与传动轴外表面也是过盈配合,故套圈的配合面处均按固支对待。经ABAQUS有限元软件处理后输出质量矩阵和刚度矩阵,然后用广义的Collatz包含定理求出它的低阶固有频率。
由于套圈是直接承受齿轮传动装置箱体动态激励力的零件,且电阻应变片是直接粘贴其上的,因此套圈的共振将直接反映在动态应变信号中。为了准确无误地从动态应变信号中诊断出传动零件的故障信息,必须预测套圈的径向振动固有频率。
套圈是一个不规则的零件,先用有限元按三维八节点实体单元对它进行网格划分,图3-7是有限元网格划分图。边界条件是这样处理的:由于套圈装在减速机箱体孔中时,和孔的配合是过盈配合,且套圈内表面与传动轴外表面也是过盈配合,故套圈的配合面处均按固支对待。经ABAQUS有限元软件处理后输出质量矩阵和刚度矩阵,然后用广义的Collatz包含定理求出它的低阶固有频率。
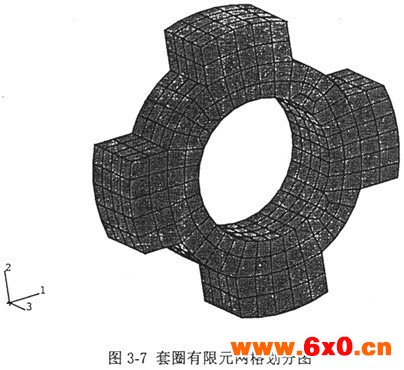
广义特征值的Collatz包含定理计算公式如下:
对于由质量矩阵和刚度矩阵构成的广义特征值问题
MX=λKX (3-7)
Crandall中和胡海昌都指出了Collatz定理不适用于广义特性值问题,若化成标准特征值问题
DX=μX,μ=
(3-8)
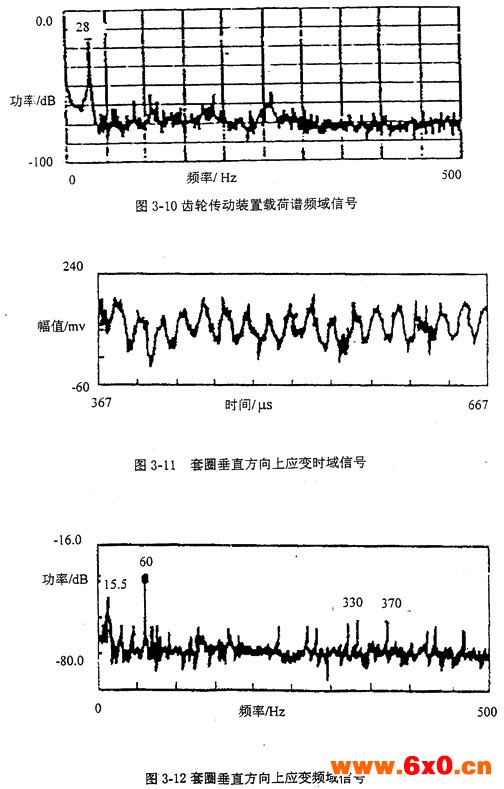
由于动力矩阵D=M-1K不再具有对称性,因之Collatz包含定理不再适用,当M为对角矩阵,矩阵D仍为对称矩阵,因此化广义特性值问题为对称矩阵的标准特征问题,Collatz包含定理仍适用。
按通常的矩阵迭代法,一般也避免矩阵的直接求逆,而是采用三角分解。下面按刚度矩阵K正定情况讨论:
K=LLT
令
y=LTX
代入(6)式,并前乘L-1,得
L-1ML-1y=λL-1LLTL-Ty
于是得标准特征值问题
Ay=λy (3-9)
其中
A=L-1ML-T (3-10)
当求得了套圈的质量矩阵和刚度矩阵后,利用前面的公式编程进行迭代计算,求得套圈的一阶振动固有频率f=935.46Hz
3.4.4齿轮传动装置故障振动诊断特征参数及动态应变信号分析
齿轮传动装置中传动零件在发生故障时,其振动时域波形、振动频率成份及振动能量都将发生改变。一般来说,利用振动时域波形的变化可精略地诊断传动零件发生故障的情况,但要更准确地诊断传动零件发生故障的情况,必须利用频域参数及振动能量或功率的变化来进行分析。这里采用齿轮传动装置传动零件可能发生故障的振动频率(具体计算公式见第4章)及其振动频率处的功率作为故障诊断特征参数,通过分析应变信号的频率成份和振动频率处的功率大小较准确地诊断传动零件发生故障的情况。
图3-8是齿轮传动装置信号分析流程图,用HP3562动态数字分析仪采集MR-30磁带记录仪纪录的二级圆柱斜齿轮减速机试验过程中的模拟信号,可得到齿轮传动装置载荷、齿轮传动装置箱体动态激励力应变变化的时域信号,对此信号作FFT变换,可得到载荷谱和动态激励力应变变化时域信号的功率谱。为了防止功率谱泄露,在作FFT变换时,需作加窗处理,由于试验采集的是随机信号,故加汉宁(Hanning)窗处理。利用故障诊断特征参数一传动零件可能发生故障的振动频率及其振动频率处的功率对试验信号进行诊断分析。当功率谱所包含的频率成份难以区分时,可采用倒谱分析。
图3-8是齿轮传动装置信号分析流程图,用HP3562动态数字分析仪采集MR-30磁带记录仪纪录的二级圆柱斜齿轮减速机试验过程中的模拟信号,可得到齿轮传动装置载荷、齿轮传动装置箱体动态激励力应变变化的时域信号,对此信号作FFT变换,可得到载荷谱和动态激励力应变变化时域信号的功率谱。为了防止功率谱泄露,在作FFT变换时,需作加窗处理,由于试验采集的是随机信号,故加汉宁(Hanning)窗处理。利用故障诊断特征参数一传动零件可能发生故障的振动频率及其振动频率处的功率对试验信号进行诊断分析。当功率谱所包含的频率成份难以区分时,可采用倒谱分析。
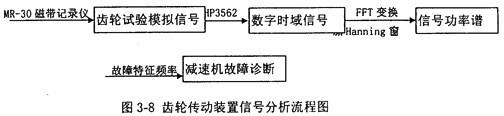
图3-9和图3-10分别是称重传感器测出的由磨擦加载装置旋加给齿轮传动装置载荷时域和频域信号(功率谱)。从图3-9和图3-10可看出,载荷主要分量是频率为28Hz正弦流。图3-11和图3-12分别是套圈垂直方向上应变时域和频域信号(功率谱)。
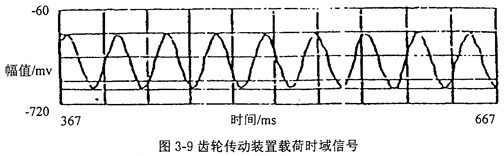
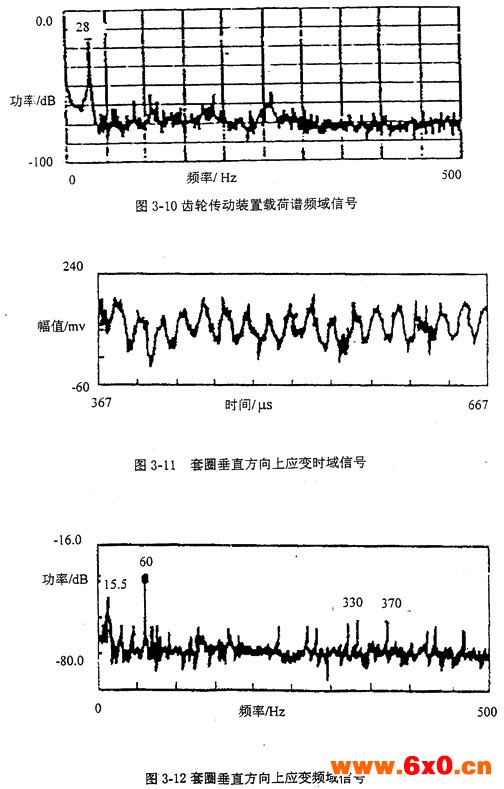
3.4.5试验结果分析
利用传动零件故障特征参数(振动频率及振动频率处的功率)对图3-12进行分析表明,可看出从套圈上拾取的动态应变信号中,振动功率位居前四位的故障频率分别是60Hz、15.SHz、330Hz和37OHz。根据计算,可以看出它们分别接近齿轮副二的啮合频率62.85Hz、轴I的轴频15.52Hz、齿轮副一的啮合频率310.33Hz和轴I的一倍轴频15.52Hz及四倍轴频62.08Hz的调制。从图3-12中也可看出,主要振动频率成份60Hz、15.5Hz、33OHz和37OHz等和套圈的径向振动一阶固有频率理论计算值935.46Hz相差较远。因此从故障振动频率分析,可以初步判定故障发生在齿轮副二、轴I和齿轮副一处。从故障振动频率处振动功率大小来分析,齿轮副二处发生的故障程度最严重,轴I次之,齿轮副一处发生的故障程度最轻。对照前面分析的故障类型与振动频率的相关性,可判断出:
(l)齿轮副二处齿轮的精度较低、齿轮的基节偏差和齿形误差较大,且较齿轮副一处齿轮的基节偏差和齿形误差大;
(2)由于功率谱中,只有轴I的一倍轴频,而没有轴I的两倍和三倍轴频,因此可以排除轴I上出现裂纹的可能性,轴I上只有可能有零件发生质量偏心。实际情况是轴I上确实有一偏心的弹性联轴节:
(3)齿轮副一处齿轮的基节偏差和齿形误差也有些大;
(4)套圈没有发生共振,套圈参数设计合理:
(5)由于信号中没有滚动轴承的故障振动频率出现,故可判定滚动轴承没有发生故障。实际情况是滚动轴承是E级的精度,精度较高,没有出现故障振动频率。
利用传动零件故障特征参数(振动频率及振动频率处的功率)对图3-12进行分析表明,可看出从套圈上拾取的动态应变信号中,振动功率位居前四位的故障频率分别是60Hz、15.SHz、330Hz和37OHz。根据计算,可以看出它们分别接近齿轮副二的啮合频率62.85Hz、轴I的轴频15.52Hz、齿轮副一的啮合频率310.33Hz和轴I的一倍轴频15.52Hz及四倍轴频62.08Hz的调制。从图3-12中也可看出,主要振动频率成份60Hz、15.5Hz、33OHz和37OHz等和套圈的径向振动一阶固有频率理论计算值935.46Hz相差较远。因此从故障振动频率分析,可以初步判定故障发生在齿轮副二、轴I和齿轮副一处。从故障振动频率处振动功率大小来分析,齿轮副二处发生的故障程度最严重,轴I次之,齿轮副一处发生的故障程度最轻。对照前面分析的故障类型与振动频率的相关性,可判断出:
(l)齿轮副二处齿轮的精度较低、齿轮的基节偏差和齿形误差较大,且较齿轮副一处齿轮的基节偏差和齿形误差大;
(2)由于功率谱中,只有轴I的一倍轴频,而没有轴I的两倍和三倍轴频,因此可以排除轴I上出现裂纹的可能性,轴I上只有可能有零件发生质量偏心。实际情况是轴I上确实有一偏心的弹性联轴节:
(3)齿轮副一处齿轮的基节偏差和齿形误差也有些大;
(4)套圈没有发生共振,套圈参数设计合理:
(5)由于信号中没有滚动轴承的故障振动频率出现,故可判定滚动轴承没有发生故障。实际情况是滚动轴承是E级的精度,精度较高,没有出现故障振动频率。
3.5小结
(l)ICP加速度传感器由于把压电传感器和阻抗变换器做在了传感器中,因而传感器的输出为低阻抗的电压,信号传输距离远,稳定性好、可靠性高,是一种值得推荐使用的加速度传感器。
(2)在确定加速度传感器安装位置时要进行反复对照比较,这个可通过振动试验来完成。既要考虑传感器安装位置合适,又要考虑该位置刚度相对要大,以确保齿轮减速机内传动件故障信号的正确处理拾取、振动较强烈。
(2)在确定加速度传感器安装位置时要进行反复对照比较,这个可通过振动试验来完成。既要考虑传感器安装位置合适,又要考虑该位置刚度相对要大,以确保齿轮减速机内传动件故障信号的正确处理拾取、振动较强烈。
(3)在齿轮传动装置的轴承外圈套圈上拾取的应变信号能直接全部反映齿轮传动装置内的轴系部件(或称传动零件)的故障振动信号,利用故障诊断特征参数一传动零件的故障振动频率成份和频率处的功率对此信号进行分析,可对齿轮传动装置内的轴系部件进行正确的故障诊断。
(4)在可能影响齿轮传动装置箱体振动的各种因素中,当齿轮的基节偏差和齿形误差大即齿轮的精度比较低时,从套圈上反映出的齿轮故障对动态激励力的影响特别明显,动态激励力的功率谱中以齿轮啮合频率及其与所在轴轴频相调制的频率为特征的谱峰最为特出。此外,在多级齿轮传动中,如果那一级齿轮副的加工精度越低,套圈上的应变信号的功率谱中以该级传动齿轮副的齿轮啮合频率为特征的谱峰更为特出。
(5)以齿轮传动装置的传动零件故障振动频率成份内容和频率处的功率大小作为故障诊断特征参数对动态应变信号进行分析和故障诊断,可以基本诊断出包括传动零件加工误差一质量偏心在内的传动零件所有故障。
(6)搞清楚传动零件故障振动频率成份和传动零件故障的相关性是搞好齿轮传动装置故障诊断的基础。
(7)本试验方法简单,成本低,对加速度传感器无法安装到齿轮传动装置轴承座附近的信号拾取及设备的故障振动诊断是一种新方法,值得推广使用。缺点是当套圈被激起共振激烈时,传动零件的故障振动信号反而会被淹没。因此在设计套圈结构尺寸时,要尽可能避开传动零件的故障振动频率。
(4)在可能影响齿轮传动装置箱体振动的各种因素中,当齿轮的基节偏差和齿形误差大即齿轮的精度比较低时,从套圈上反映出的齿轮故障对动态激励力的影响特别明显,动态激励力的功率谱中以齿轮啮合频率及其与所在轴轴频相调制的频率为特征的谱峰最为特出。此外,在多级齿轮传动中,如果那一级齿轮副的加工精度越低,套圈上的应变信号的功率谱中以该级传动齿轮副的齿轮啮合频率为特征的谱峰更为特出。
(5)以齿轮传动装置的传动零件故障振动频率成份内容和频率处的功率大小作为故障诊断特征参数对动态应变信号进行分析和故障诊断,可以基本诊断出包括传动零件加工误差一质量偏心在内的传动零件所有故障。
(6)搞清楚传动零件故障振动频率成份和传动零件故障的相关性是搞好齿轮传动装置故障诊断的基础。
(7)本试验方法简单,成本低,对加速度传感器无法安装到齿轮传动装置轴承座附近的信号拾取及设备的故障振动诊断是一种新方法,值得推广使用。缺点是当套圈被激起共振激烈时,传动零件的故障振动信号反而会被淹没。因此在设计套圈结构尺寸时,要尽可能避开传动零件的故障振动频率。