针对壁板类组件的装配,国外多采用多点阵真空吸盘柔性工装,采用“N-2-1”的定位方法,通过控制吸盘的三维移动定位,生成与壁板组件曲面完全符合并且分布均匀的吸附点阵,从而可靠地定位和夹持壁板[5-9]。目前,国内在实际生产中仍然大量使用“一对一”式的传统刚性工装,采用卡板以内/外形定位的方式定位壁板组件,每套壁板组件对应的工装都需单独设计制造,工装缺乏对壁板产品变化的快速响应能力,工装制造成本高、准备周期长、误差累积较大[3-4]。针对这一问题,柔性壁板装配工装在现实中已经得到初步应用[10-15]:王亮等[10]提出了一种卡板定位支点可重构的数控柔性多点型架的方法,通过移动卡板装配点位置,结合可更换的卡板,实现在飞机装配中一个型架用于多种壁板类组件的装配模式,但其仍采用大量外形卡板的定位方式,延续的仍是传统刚性工装的设计思路,当产品对象更改时,更换后的卡板工作外形安装精度难以保证,装配准确度较低;李东升等[11]描述了一种行列吸盘式壁板装配柔性工装,工装中的每个吸盘在电机控制下能够实现空间三维的定位,构成不同外形点阵可满足对各种外形壁板的吸附定位。虽然不再使用卡板定位,能够满足数字化、柔性化装配要求,但结构过于复杂,制造安装困难,另外,X和Z向移动通过同步带传动,导致外廓尺寸较大,同时同步带齿易折断、磨损,需经常更换。Lu[14]、陆俊百[15]等对用于飞行器薄壁件柔性工装定位阵列优化自动生成进行研究,通过分析系统结构和运行原理,采用“N-2-1”的定位方法,解决了工装定位曲面的快速生成和相应的优化控制等关键技术,已应用于大型薄壁件的加工。
为解决当前飞机壁板类组件装配工装重构性弱、定位精度低、通用性差及卡板依赖性强等问题,本文根据机身壁板的结构,分析其装配需求,采用“N-2-1”的定位方法,研制了面向机身壁板的数字化柔性装配工装。通过设计相关承载立柱,采用专用定位器夹持壁板边界,由多个真空吸盘吸附壁板内表面,并使用PLC+IPC(可编程控制器+工业计算机)的控制系统,驱动伺服电机运动调整定位器和吸盘的定位布局,实现了机身壁板装配的数字化和柔性化。
机身壁板装配需求分析
机身壁板主要由蒙皮、长桁等弱刚性薄壁件组成,按照特定的位置关系铆接成为一个整体结构。蒙皮作为壁板的主要构件,为刚性较差的弹性薄壁件,具有尺寸大、形状复杂及易变形的特点,需用定位器保持其外形轮廓;长桁一般为“Z”形或“J”结构,在长桁外形面及蒙皮上取预装配孔,按装配孔沿蒙皮母线方向定位装配[1-3]。结合数字化、柔性化装配的要求,使用数字量的尺寸与形状传递方式,采用钻孔机器人完成蒙皮与长桁的制孔,实现不同曲率机身壁板对象组成零件的预装配定位工作,以保证飞机壁板的高精度装配要求,文中根据机身壁板结构特点,为实现不同壁板定位布局的快速转换,满足不同壁板的定位需求,机身壁板组件柔性装配需求如下:
(1)根据壁板在工装中定位完成后,采用钻孔机器人完成蒙皮与长桁制孔时的开敞性需求,需以蒙皮内形为装配基准,采用内定位的装配定位方式。
(2)为满足壁板在工装上定位的稳定性,采用“N-2-1”的定位方法(壁板内表面由多个蒙皮内形定位点进行定位,壁板下侧水平边界由两个定位点进行定位,壁板竖直边界由一个定位点进行定位),在三维模型中均匀划分壁板定位区域并在壁板范围内均匀布置壁板定位点,布置定位点过程中必须使其避开长桁及蒙皮内表面存在台阶的区域,从而保证每个定位点均可对壁板进行稳定的定位。
(3)为实现对不同蒙皮内形的定位点进行定位,结合真空吸盘吸附的稳定性[5-9],采用真空吸盘对蒙皮内形进行定位。
(4)针对不同曲率的机身壁板的装配要求,需配以不同角度的吸盘安装板,以保证真空吸盘的吸附夹持效果。
(5)为了实现不同尺寸的壁板组件的柔性定位要求,壁板组件承载立柱各运动方向的定位夹持单元须可以沿水平与竖直方向独立运动;同时每个可移动的蒙皮内形定位夹持单元能够独立伸出移动,以保证工装能够满足不同弦高的机身壁板装配要求。
工装机械结构设计
1工装工作原理
根据机身壁板结构特点,结合壁板组件装配需求,融合模块化设计思想[16],设计以蒙皮内表面为装配基准的数字化柔性装配工装,如图1所示。工装主要包括基座模块、立柱模块、蒙皮边界定位夹紧模块、蒙皮表面定位夹紧模块。工装采用“N-2-1”原则定位壁板,即壁板内表面由多个蒙皮内形定位点进行定位,壁板下侧水平边界由两个定位点进行定位,壁板竖直边界由一个定位点进行定位。通过数字伺服控制系统调整定位器的布局,形成不同的吸附点阵可以满足不同壁板的装配要求,实现工装“一架多用”的功能。
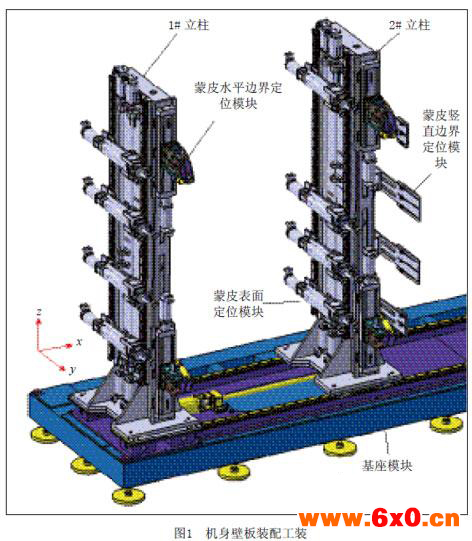
2工装结构设计
基座为多点可调支撑底座,由12个均匀分布的调平螺栓支撑,能够有效应对地基变化对工装的影响。基座上方安装两个承载立柱,1#立柱在X方向上固定不动,2#立柱在伺服电机驱动下可沿X方向移动。立柱左侧安装蒙皮表面定位夹紧模块,立柱前端面安装蒙皮水平边界定位夹紧模块,2#立柱右侧安装蒙皮竖直边界定位夹紧模块,如图2所示。
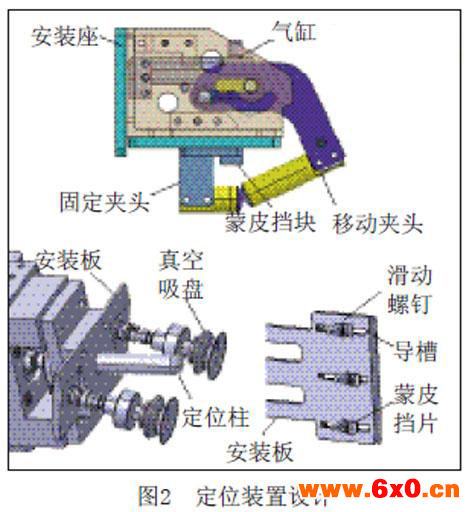
蒙皮表面定位夹紧模块由真空吸盘、吸盘安装板、定位柱、Y向驱动单元和Z向驱动单元组成。吸盘安装板上安装两个真空吸盘(可进行周向±15°角度补偿),为保证吸盘的吸附夹持效果,可根据壁板的曲率选择不同角度(0°和15°)的安装板进行安装,定位柱通过自身螺纹安装于吸盘安装板中部。吸盘在电缸的驱动下可在Y向移动,电缸安装在可上下运动的托板上,在伺服电机驱动下可在Z向移动。选择不同的吸盘安装板能实现±30°的角度偏转可满足不同曲率的壁板的装配要求,调整吸盘在Y向的位置可适应不同弦高的壁板装配要求。
蒙皮水平边界定位夹紧模块由蒙皮夹紧装置和Z向驱动单元组成。蒙皮夹紧装置主要包括固定夹头、移动夹头、蒙皮挡块和连接板等,固定夹头、移动夹头和蒙皮挡块通过连接板组合在一起。蒙皮挡块起定位作用,通过固定夹头和移动夹头的相对移动夹紧蒙皮,其中移动夹头的运动由气缸带动。蒙皮夹紧装置安装于Z向集成模块上,在伺服电机驱动下可在Z向移动。蒙皮夹紧装置在Z向的运动能满足不同宽度的壁板的装配要求。
蒙皮竖直边界定位模块由滑动螺钉、安装板和连接座组成,主要用来定位蒙皮在X向的位置。滑动螺钉上安装蒙皮挡块,调节螺钉在安装板水平导槽中的位置来适应不同曲率的蒙皮,安装板通过连接座固定在在2#立柱右侧面。在X向有效行程范围内,改变2#立柱在X向的位置,可满足一定长度范围内壁板组件的稳定性与柔性装配。
3装配误差分析
在实现壁板组件的柔性装配过程中,为保证装配准确度,要控制的误差环节主要包括以下方面。
(1)工装定位误差。
工装的定位误差是指立柱定位单元的定位执行末端从设定的原点位置出发,沿3个相互垂直的方向运动到理论空间位置后,定位器上定位基准的实际空间位置与理论位置的偏差。在定位单元运行调试过程中,定位单元不承受外部载荷,但其运行工况、制造精度、安装精度、几何精度、测量精度与控制系统精度等因素均对定位有影响,其中,定位单元运动部件的几何精度所产生的定位误差是影响定位执行末端定位误差的zui主要因素[17],主要包括各运动方向的滚珠丝杠传动系统的轴向定位误差与其导程误差、导轨导向传动系统的安装定向误差对定位基准点产生的定位误差。根据此3类误差源建立柔性工装立柱定位单元单轴运动的定位误差模型,并根据可叠加性原理对综合定位误差进行综合计算。经误差补偿后,立柱定位单元模块的定位精度方可满足工程中对飞机部件的定位精度要求。
(2)零件制造误差。
零件制造误差是装配误差中的重要成分,其取决于形成零件zui后形状和尺寸的尺寸传递过程中的各个环节,即装配协调路线。在数字化装配环境下,整个尺寸与形状传递过程以飞机产品设计数学模型为依据,经机械加工工艺设计及后置处理后,将产品的几何形状与容差信息通过数字量形式存在的NC加工指令直接传递给数控加工设备,形成物化的零件,经数字测量设备检测合格后,即可进行产品的装配工作。
(3)产品在工装中的协调误差。
在飞机壁板类组件的装配过程中,会受到夹持力、钻孔力、连接力、回弹力等的作用,由于本身刚性不足,在外力作用下会产生一定的变形,当外力释放后,又会产生一定的变形回弹量,各种外力产生的变形量在装配过程中相互影响,将引起装配不协调、装配超差等问题。同时,定位误差在装配过程中影响各装配环节,导致误差进一步放大。因此,针对壁板类组件的装配,需要详细分析其定位过程与实际装配工况,采用合理有效的方法得到个阶段的定位误差,获取其装配变形误差,建立正确的耦合算法,综合这两类误差之间的影响关系,进而获取zui终的装配误差。
工装控制系统设计
柔性工装的自动重构主要依赖控制系统,它将完成壁板装配过程中所需各种运动定位器的定位,实现工装对壁板的可靠固定,保证机身壁板外形与数字化样机的一致性[18-20]。
1硬件系统设计
壁板装配工装的控制是一种典型的以位置控制为目的的数字化控制系统,涉及到机、电、气等多种系统的集成控制[21]。工装包括12个定位调整单元,由21个伺服电机驱动控制,属多轴运动控制。
工装控制系统运行时,上位机将驱动程序发送给控制器,控制器通过现场总线将信息传送给各驱动器,驱动器驱动电机完成运动指令。电机编码器实时监测运动状态,将位移、转速等数据发送回驱动器,构成半闭环控制系统。同时,借助数字化测量设备(激光跟踪仪)实时测量工装上定位基准点的位置信息,将实测数据与理论数据进行对比,如果不在误差允许范围内需进行运动补偿。所有基准点完成定位后即可将蒙皮夹紧,进行制孔铆接等操作。
2软件系统设计
控制系统软件包括两部分:底层软件(运动控制)和上层软件(人机交互)。文中主要说明上层人机交互软件,包括系统初始化模块、用户管理模块、工艺控制模块、运动控制模块、气动控制模块。
系统初始化模块为用户登录及软件启动时的参数初始化;用户管理模块是用来对用户信息进行管理;工艺控制模块是工装控制系统的软件柔性化的体现,即通过运行不同的工艺,完成不同壁板的定位,工艺编辑是对工艺内容进行编辑,工艺运行是使工装各运动轴按照预设的工艺顺序执行;运动控制模块是手动操作部分,包括设置电机的参数(速度、加速度、位置等)及单轴动作(定零、回零、暂停/继续等);气动控制模块是在各基准点准确定位后,完成蒙皮的夹紧动作。软件界面如图3所示。
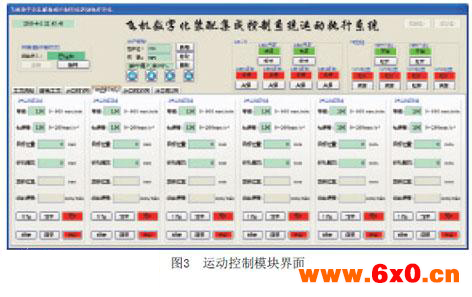
机身壁板组件装配定位方法
根据设计的机身壁板工装机械结构和控制系统,为实现壁板组件的柔性定位,所采用的技术方案如下:
(1)根据工装和壁板三维模型及其结构和尺寸,结合装配工艺,规划各定位点运动路径,并使定位点在壁板范围内均匀分布。
(2)在三维CAD装配环境中,设定工装装配基准坐标系,根据工艺顺序进行装配仿真并检查是否有干涉,对干涉部分进行检查修改,通过装配仿真获得各定位点在装配基准坐标系中的坐标。
(3)对上述获取的定位点坐标进行转换,生成工装各运动轴可用的数控代码,利用控制系统使工装各定位点按照工艺顺序运动到指定理论位置。
(4)测量各定位点在工装坐标系中的实际位置,得到实际坐标与理论坐标的误差值,把此误差值反馈到控制计算机,计算生成坐标补偿量,再利用控制系统对定位点进行移动补偿,以保证各定位点的位置偏差在允许误差范围内。
(5)先把机身壁板落放在下侧水平边界定位点上以保证壁板竖直方向上的定位,水平移动壁板直至与竖直边界定位点接触以保证壁板水平方向的定位,把壁板内表面靠近已生成的与蒙皮曲面完全符合的真空吸盘吸附点阵,通气后完成蒙皮的吸附工作,并对壁板边界用夹紧装置进行夹持,完成对壁板内形的完整定位。
(6)采用钻孔机器人完成蒙皮与长桁的制孔工作。
结论
本文针对传统壁板装配方法,借鉴国外多点阵真空吸附柔性工装,根据机身壁板的结构,采用“N-2-1”定位原则,设计机身壁板数字化柔性装配工装,通过控制系统调整吸盘及夹紧装置的位置以满足不同种类壁板的装配要求,其安装现场如图4所示。其应用可以减少专用刚性型架、缩短研制周期、通过数字量的协调传递提高装配质量和生产效率,具有推广价值。
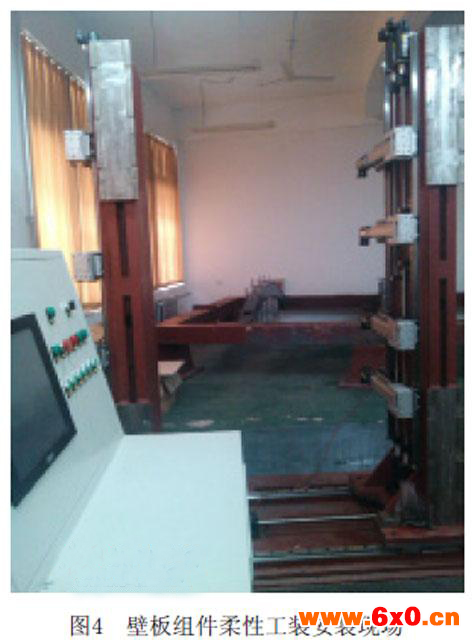
(文章来源:西北工业大学机电学院)