钣金件成形对模具的技术要求
现代飞机对气动外形要求严格,对钣金件的要求不止是贴合,更要有稳定的质量和性能状态。对钣金零件的表面质量、形状精度、成形过程稳定性、成形性能以及产品合格率等要求日益提高。如波音747-8项目,其机翼外形相对理论外形的偏差一般不小于0.5mm,不平滑度小于0.05~0.15mm,钣金件弯边高度的精度要求控制在-0.1~0.2mm。目前钣金成形航空模具的传统加工方法主要是按外形样板+特种角度样板或正反模形垫料后取过渡模协调制造,这种工艺方法制造出的模具外形误差可达到0.2~0.3mm,局部达到0.5mm以上。所以,提升钣金成形技术水平,必须要提升钣金成形模具制造数字化技术。
与传统模具制造技术相比,钣金成形模具数字化制造技术要求更加复杂。*,钣金成形模具外形型面的复杂程度[1],塑性变形特点和成形回弹等因素不仅涉及到其零件本身数字化定义,还包括毛坯、下料、成形工序、成形工艺数模等定义;第二,钣金成形模具制造过程中,其塑性变形的非线性所带来的不*性、不可逆性等引起的工艺上的参数不确定性,都影响着钣金成形模具的质量和效率。
传统的航空模具加工方法及存在的问题
以波音747-8项目为例,65B03524-49/50零件是一项钣金成形件,现有制造工艺方法一般为模拟量技术传递工艺加工技术(即按外形样板)和特种角度样板制造航空模具的方法,具体方法有2种。
(1)按外形样板。靠模在数控靠模铣上用靠模头扫描靠模存盘,然后调出存盘的数据加工模具。
(2)按飞机的正、反模形垫料厚取制靠模,按靠模在数控靠模铣上用靠模头扫描靠模存盘,然后调出存盘的数据加工模具。
在基于模拟量传递为主的钣金件制造模式中[2],存在以下问题:
(1)钣金件设计模形虽准确描述了zui终的形状和尺寸,但未考虑钣金件工艺过程的中间状态,无法解决设计信息向制造延拓的矛盾。
(2)按样板制造靠模、靠铣工铣过的航空模具型面一般还留有0.5~3mm余量,且余量不均,钳修量非常大。现实生产中急需找到一种对类似模具具有较高精度的加工方法。
总之,钣金件制造工艺过程各环节的几何形状缺乏严密的数字定义,零件制造准确度难以保证。
数字量的传递加工方法
在航空钣金成形模具制造中数字化技术的核心是数字量的传递加工方法。其主要通过面向工艺过程定义工件模形和工艺模形,移形到模具上生成数控程序,以数字量传递到数控设备这样一个并行数字化制造过程。这个过程的实质在于毛坯组合排样模形、成形工艺模形等下料、成形各控形节点中的CAD几何模形直接用于成形模具设计制造指令设计、工艺参数设计和数控加工程序建模等环节,能在样板制造、模具制造中始终保持给定的公差。这就消除了模拟量传递的若干环节引起的累积误差,减少了人为不确定因素的影响,改变了反复修错的制造方法,从而实现精密、快速和低成本的制造。
数字化制造技术在闸压模中的运用案列
以波音747-8项目中的框肋成形零件为例,采用基于制造模形的数字量传递方法,闸压模具型面设计依赖于制造模形中的成形工艺模形而不是直接依赖于零件原始数模。成形工艺模形考虑了零件回弹等因素,并且给出了修正方案及修正参考值,对于型面和尺寸进行了合理的预修正。
1数据测量
1.1用便携式测量臂测量样板生成数据
(1)将样板水平地放在平台上,用便携式测量臂的探头尽量的贴着样板的外形侧面及平台的水平面检测样板的外形,每个点相距20mm左右,采集数据,将样板的端头外形按侧面的方法采集数据。
(2)样板的每个角度的标记处,用探头在标记处采集2个点,用以确定角度变化的实际位置,同一块样板检测2次,以确认采集的数据可靠性。
(3)样板超过便携式测量臂的检测范围时,可以用划针样板中间的位置轻轻地划一条直线,用以转换检测基准,检测完一半后,将便携式测量臂转换到新的基准上,继续检测。检测完后,将检测的数据存入文件夹。
(4)操作人员采集数据后,直接将数据存入与便携式测量臂联机的电脑内的硬盘中。
1.2利用数据生成样条
便携式测量臂采集的数据多,如何将大量的数据导入建模软件,可以采用以下方法:首先,利用UG软件上的程编室工具的读文件点的功能,使这大量的数据点较便捷地导入建模软件成为可能;其次,将采集的数据用Excel软件进行处理,将点位数据导入Excel软件,生成文档文件,将这些点位数据按先后次序排序,并生成排位号,在Excel文件中添加I、J、K,在I、J、K的下面数据可以全部是0,将点集成文件存为后缀.MDA的有序文件;再次,用UG的读入文件的接口,将生成的文档文件读入,并由UG的曲线功能将这些点连成曲线,将点集串成样条、光华流顺;zui后,将UG的文件另存为后缀为.igs的文件,样条生成过程如图1所示[3]。
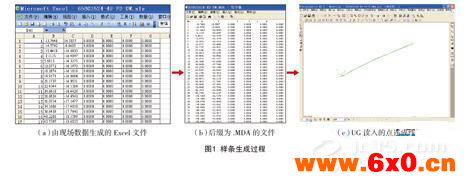
(1)CATIA将由UG保存的后缀为.igs的文件读入[4]。该零件为异形材料,厚度较大,成形时零件存在反弹。将反弹角设计为6°较为合理,建模时注意下限处的反弹角按一个点旋转。
(2)样板的每个角度变化处,按角度的变化值做出零件的截面,省略零件的T形值的凸筋,然后将各截面光顺地连接起来。
(3)将各截面拉成零件,零件的成形面建模后的形状,利用抽取零件下表面形成的面,裁剪实体,形成闸压模的下模,并按零件凸筋的厚度将下模一分为二,形成左、右下模,左、右模中间的垫板与右下模做成一体的(图2)。
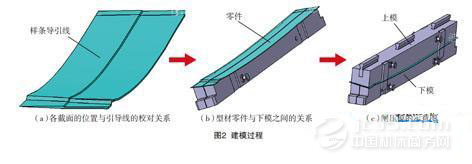
(4)利用抽取的零件上表面形成的面,裁剪实体,形成闸压模的上模,上模的顶面开出模柄安装槽,上、下模的两侧面开出导板安装槽,上、下模与零件组合为组合件,安装上模柄、起吊螺栓、导板,一套完整的闸压模就完成了建模图。
3UG软件编程
(1)用UG软件编制加工程序时,要注意加工出样板检查时使用的基准面[5],加工出导板的安装槽,并且加工出端头定位面。加工的原点设在底面与样板基准面、端头定位面交汇处,这样就可以保证上、下模型面的相对位置,但编制加工时的模具的表面光顺度还有待提高(图3)。
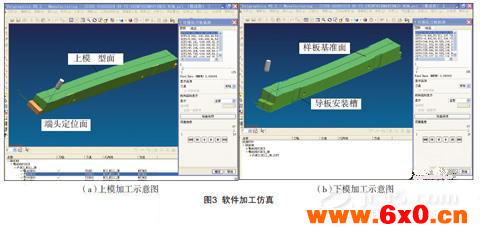
(2)2件下模分别粗加工后,加工侧面的导板滑动槽时,一定要制出下模的合模销孔,保证下模之间型面的相对位置正确。
4检测和修模
3D的建模只是替代了人工制造的靠模,数控加工只是替代了靠模加工,由于模具的制造依据仍然是外形样板,检验是按外形样板及特种角度样板交检的,数控加工只是近似加工,近似加工与zui终成形的模具的相似程度,取决于对样板的理解及3D建模的水平,还取决于数控加工的操作者严格按程序单的要求,认真地加工出样板的定位面,只有这样才能将数模与样板结合起来。这种数控加工出来的粗坯与实际需要的状态非常接近,减轻了钳工的劳动强度,提高了制造精度[6]。
结束语
本文以框肋成形零件为例,重点讲述了闸压模数字化设计、制造的整个过程,同时提供了相关的模具成形工艺方面的实际经验。数字化技术在航空钣金成形模具制造中的应用对于提高航空制造企业的经济效益具有非常重要的意义。
(文章来源:航空制造网)